Capps Manufacturing in Wichita, KS, fabricates roll formed sheet metal parts for military, business and commercial aircraft. With more than 40 years of industry experience, our capabilities include rolled and stretch formed aircraft sheet metal parts for customers around the world.
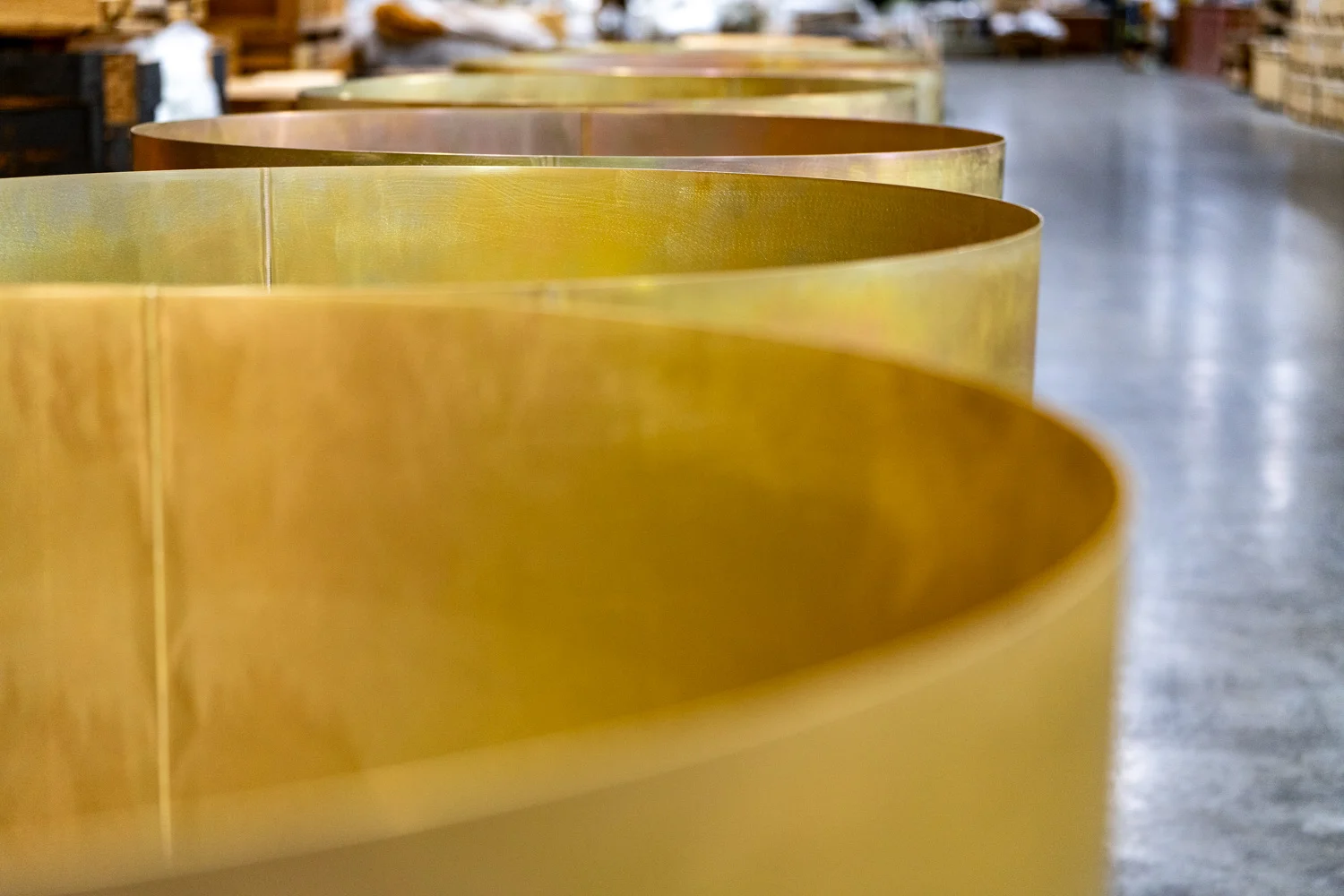
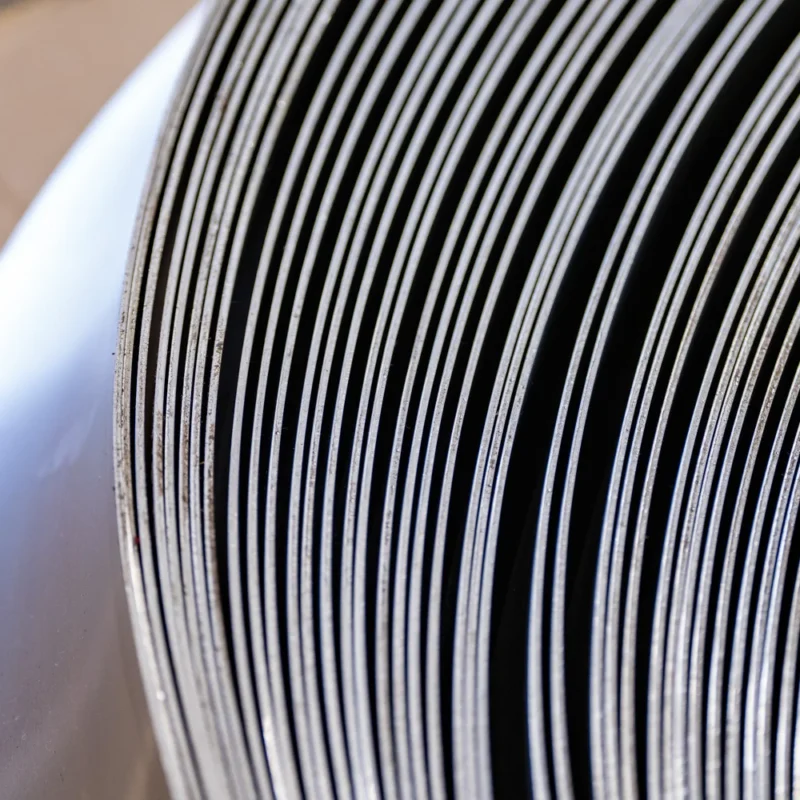
What Is Roll Forming?
Roll forming is a metal forming process. It shapes sheet metal through multiple bending operations.
Roll Forming Uses
With tight tolerances of ±0.005 inches, the roll forming process can produce precise parts commonly used in the aerospace industry. Roll forming is used to make long sheet metal parts with widths of 1-20 inches and thicknesses of 0.004-0.125 inches. Some sheets can be even wider and thicker, up to 5 ft. wide and 0.25 inches thick.
The roll forming process can create different cross-section profiles from a sheet. It can make open profiles or closed tube-like shapes. The final shape doesn’t need to have a uniform or symmetric cross-section along its length because it’s formed through a series of bends.
How Roll Forming Works
Roll forming takes place on a roll forming line. In this line, the sheet metal stock moves through several roll stations. Each station has a roller die on both sides of the sheet. The roller die can be unique to the station or the same roller die can be used in different positions. The roller dies can be positioned above, below, along the sides, or at an angle to the sheet. When the sheet passes through the roller dies in each roll station, it bends and deforms. Each roll station contributes to forming the desired part.
To reduce friction and tool wear, the roller dies are lubricated. Lubricant also helps increase production rate, which depends on material thickness, number of roll stations, and bend radius. The roll forming line may also include other sheet metal fabrication operations like punching or shearing, before or after the roll forming.